Completed: Low-temperature densification of α-Al2O3 through a modified cold-sintering process
In collaboration with Johnson Matthey
α-Al2O3 is a technical/advanced ceramic used in applications such as electrical insulation, wear, and corrosion resistance, with approximately 120,000 metric tonnes manufactured per year worldwide. Conventional processing of α-Al2O3 ceramics requires significant effort in optimising physical powder characteristics through reduction in particle size, followed by sintering at ~ 1600°C to achieve the required densification. In this project, the technique of cold-sintering was considered as an aid to densification, the aim being to reduce significantly the sintering temperature thereby offering significant energy savings in processing and also decreasing the intrinsic costs of infrastructure and capital equipment (furnace and element technology is far less stringent when densification can be achieved at ≤1400°C).
Pseudo-boehmite (Al(O)(OH)n) is a low cost raw material used in the fabrication of alumina powders. It decomposes on heating to form a alumina at >1100°C after passing through a complex sequence of phase transitions. It can be functionalised as a prelude to cold sintering using ~1 molar acetic acid to form a surface coating of acetate-alumoxane powder. The functionalised powder may then be cold sintered to near 100% dense if required but in this study the pseudo-boehmite was mixed with a-Al2O3 and aluminium nitrate to form cold sintered dense composites which could subsequently be heat treated to form a-Al2O3 pellets. A range of pressure, cold sintering temperatures and boehmite/a-Al2O3/aluminium nitrate ratios were studied and the phase assemblage and densification investigated.
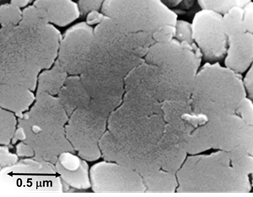
Although fully dense a-Al2O3 pellets were not achieved at 1200°C, large areas of the pellets had densified with evidence of 120o triple junctions in parts of the ceramic, Figure above. The absence of full densification suggests that better mixing may be required during the processing sets to ensure a homogenous distribution of the starting powders and potentially higher temperatures (even 1400°C would still offer a significant energy saving and commercial advantage in capital equipment and infrastructure). This work has been extended through a further Early Career Researcher (Beatriz Almeida) supported by the European Ceramic Society and has formed part of an Engineering and Physical Sciences Council grant submission. A comprehensive publication of the data is planned.
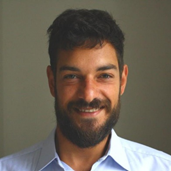
Dr. Edoardo Mantheakis
University of Sheffield
Published: October 28th, 2022
Posted in
projects