Completed: Using blast furnace waste heat to convert various wastes into new raw materials for low energy glass manufacturing
In collaboration with British Glass, Glass Futures, Calumite Ltd and the Materials Processing Institute
Energy-intensive industries such as glass manufacturing and steelmaking face significant challenges in reducing energy consumption and CO2 emissions. For example, heat during blast furnace hot metal and slag tapping dissipates into the atmosphere and is currently not recovered/utilised and, in glass manufacturing, a significant amount of energy is consumed in raw material preparation and melting with CO2 released from the decomposition of carbonates.
This project investigated the possibility of developing an innovative process for utilising the blast furnace waste heat to convert contaminated recycled glass streams to high value raw materials to reduce energy, virgin raw materials consumption and CO2 emissions. The results are considered particularly beneficial for hard-to-use/recycled wastes such as contaminated glass streams.
Mass and heat balance and thermodynamic modelling determined how much waste may be utilised and its impact on operational parameters such as melting temperature and viscosity. The results suggested that up to 50 kg waste glass may be added to 100 kg molten blast furnace slag under ideal operating conditions. The figure below shows the effect of the addition of contaminated waste glass containing 5% organic waste on the slag liquidus (green line). The liquidus temperature of the new slag decreased with increasing waste glass addition.
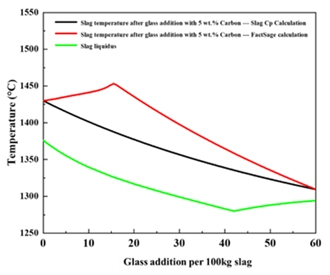
The second figure shows the impact of waste glass addition on the viscosity of new slag and demonstrates that with up to 50 kg waste glass added to 100 kg blast furnace slag at a practical operating temperature of 1400°C, the viscosity is less than 4 Pa∙S. Our data suggest therefore, that under an industrial scenario (with strong stirring caused by injection) the dissolution of waste glass will not be a limiting factor and the process is technically viable. Our findings have been shared with industrial partners during the execution of the project, who along with the PI have been exploring ways to up-scale the process.
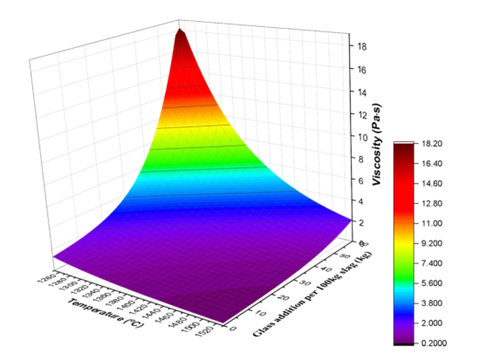
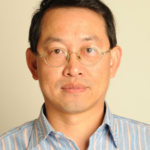
Prof. Zushu Li
University of Warwick
Email: Z.Li.19@warwick.ac.uk
Dr Zushu Li is a Reader in the Advanced Steel Research Centre (ASRC), WMG at the University of Warwick and ex-Principal Scientist Steelmaking in Tata Steel R&D. He joined WMG in 2016 with an EPSRC Manufacturing Fellowship in sustainable steel manufacturing. He specialises in multiphase high temperature reactions. At ASRC, he leads the research and development in decarbonising steel industry including alternative iron making technology, scrap utilisation, hydrogen applications in steel manufacturing, and energy and materials recovery in steelmaking.
Published: November 3rd, 2021
Posted in
projects