Completed: Investigation of a Flat Heat Pipe for high temperature waste heat recovery from metal slabs.
In collaboration with Econotherm
Energy efficiency is among the most important keys to unlock a green and more sustainable economy and a substantial amount of energy can be saved via the reuse of waste heat. Exploitation of waste heat streams has already been investigated mainly relying on forced or natural convection as a heat transfer method. However, waste heat is also available as a radiative source. Radiative heat sources pose real challenges due to the complexity of modelling, its intensity and the status of current technology. Indeed, no technology can currently effectively recover radiative waste heat sources. Brunel has developed a novel radiative Flat Heat Pipe (FHP) heat recovery system to capture high temperature waste heat such as form slags, and slabs. The FHP relies on two phase transfer to passively move heat from the hot to the condenser section. The heat is then transferred safely to the heat sink such as air, water and water-glycol. The FHP system was designed according to a thermal/electrical analogy, was constructed with the support of Econotherm Limited and prepared for testing. Testing was carried out in an industrial environment and for a heat source of 450°C. The FHP was able to recover up to 800 W/m2 with an average evaporator surface temperature of 45°C, highlighting its potential for even higher temperatures.
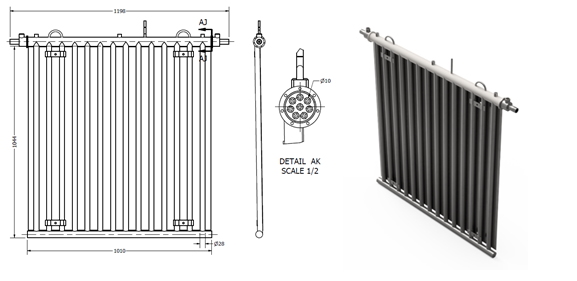
The results of this industrial test, along with validation of the FHP model, allowed Brunel to assess further potential utilisation. It was concluded that the FHP technology could be easily implemented in the steel industry, for example, in the manufacture of wire which is extruded and cooled down by forced convection and radiation on long conveyors. If applied to the entirety of the conveyor, the expected output from the FHP system is predicted to be 12.5kW/m2. The aim is to further develop the technology to full demonstration scale, initially in the metals sector which presents strong potential for FHPs due to the high temperature and available heat sinks but also in cements. The built environment relies upon the metal and cement sectors for much of its materials. Heat recovery in these energy intensive industries is of vital importance if we are to continue to manufacture in the UK. This is true irrespective of the introduction of low carbon or carbon neutral energy production in the future.
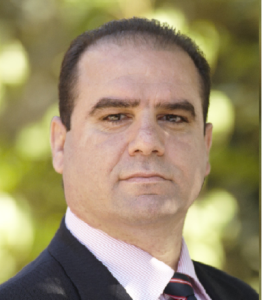
Professor Hussam Jouhara
Brunel University London
Email: Hussam.Jouhara@brunel.ac.uk
Prof. Hussam Jouhara is a Chair in Thermofluids at Brunel University London. He is the head of the Heat Pipe and Thermal Management Research Group, which hosts a multitude of research activities supported by national and international research councils. His innovative design methods have led to applications of the heat pipe technology in over 32 countries, and many granted international patents. The development of heat pipe heat exchangers, produced by Prof. Jouhara, has been applied to many industries, such as recovering waste heat from ceramics, steel industry, food processing, solar PV thermal management and thermal energy storage using phase change materials Recent major projects that deal with the development of water and heat recovery include iWAYS of which Prof. Jouhara is the scientific and technical director.
Published: November 3rd, 2021
Posted in
projects, Uncategorised